Code Green Solutions
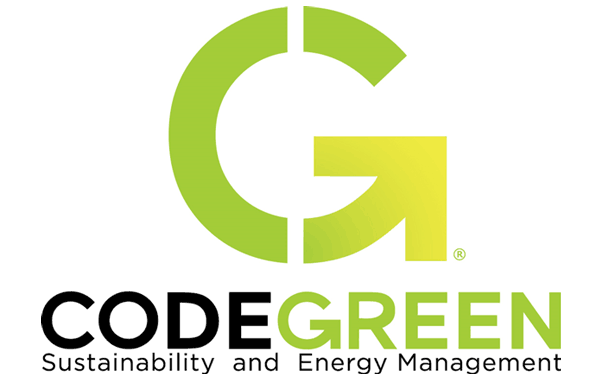
What does it mean to provide an inventory of ‘all’ the chemicals used in a product? Is it possible? Why? Why not?
It is assumed that manufacturers know every one of the chemicals in their products, but in reality this may not be so. Manufacturers do not always have complete information from their suppliers, or supplies may be contaminated unintentionally. The most common method of information about the components from a supplier to manufacturers is the Material Safety Data Sheet (MSDS). The MSDS is required by the federal government to convey the chemical safety and hazard information to the end user; however, only components that are 1% or more of the total composition (with the exception of known carcinogens, which must be reported if 0.1% or more of the composition) are required to be reported (Note: 1% = 10,000 ppm whether mass or volume). This type of limitation also exists in the transparency programs, although the reporting limits differ among the programs. For example, the minimum reporting inventory levels for several of the programs are: 1) Cradle-to-Cradle’s is 0.01% which equates to 100 ppm, 2) the European REACH is 0.1% which equates to 1000 ppm, and 3) Health Product Declaration (HPD) is 0.01% which equates to 100 ppm. As a result, there may be hazardous, irritating, strongly odorous, or toxic chemicals present in final products that have not been identified. These may be of sufficient quantities in the final product to cause a human response.
For example in one case when we were performing emissions testing of a piece of furniture – a wooden chest – the primary VOC detected in the emissions from the chest was trichloroethylene (TCE), and at high ppm levels. The manufacturer did not knowingly use TCE during the manufacture or finishing of the chest. Through a review of the component materials and querying of the component suppliers, we were able to determine that the source was a contaminant in one of the suppliers’ materials at less than 1% of the total composition of the supplied material; therefore, it was not required to be reported to the end use manufacturer on the MSDS.
In another case study, a product contained a pesticide when no pesticides had been used in or on the product, or knowingly around the product. An investigation into the pesticide source identified that the source was from the pallets on which the product had been shipped. The wooden pallets had been sprayed with the pesticide prior to being used to ship the product. Then during shipping the product had become contaminated with the pesticide.
Contamination from suppliers may not be the only source of unknown compounds in a product. Unintended reactions among components may occur. Usually manufacturers have determined these reactions, but occasionally an unintended reaction may occur due to exposure of the product to more extreme conditions than expected. For example, there are products, such as some adhesives, that contain polymeric components that are long-chained, which under selective conditions of heat and moisture exposure may decompose and release free formaldehyde or other polymerization units after application and curing. As a result, unexpected low levels (on the scale of parts per billion) may be emitting into the indoor environment. This is a phenomenon that has been dubbed “indoor air chemistry.” In general, indoor air chemistry refers to unintended reactions occurring with airborne contaminants, such as ozone and chemicals in a material, resulting in unintended contaminants being released into the indoor environment. This was originally observed and reported by Charles Weschler. He was able to detect the presence of formaldehyde and other aldehydes emanating from carpet exposed to ozone at levels similar to those found in indoor environments. Although these emissions are not originally part of the components of the material as it leaves the manufacturer, it still is a concern, since a primary goal of materials transparency is to reduce exposures from a product during use, thereby increasing the healthiness of the environment indoors.
So what is the solution? We need to continue to urge increased communication between manufacturers and their suppliers to increase purity of components going into a product, or at least better reporting of all primary and secondary components in the product being supplied. We need to increase research and understanding of potential reactions that may occur in final products, while educating on the need to maintain the manufacturer’s recommended use conditions for building materials so that unintended reaction products are prevented. Finally, we need to encourage coordination among the transparency programs so that manufacturers see the value in participation at all levels, from the suppliers to the end users, resulting in a wide spectrum of transparency useful to the manufacturing and the building industry as well as the consumer.