Code Green Solutions
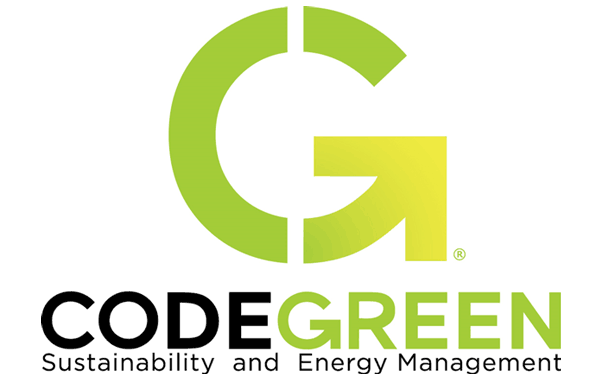
Editor’s note: This article was originally published on USGBC.org.
USGBC awarded Dagmar Epsten, LEED Fellow and CEO of Epsten Group, a LEED Platinum plaque for her LEED v4 Existing Buildings project—but it’s just part of her collection of Platinum plaques. We sat down with Dagmar to talk about her experience as a business owner and her drive to keep her company on the cutting edge of sustainability.
This isn’t your first LEED Platinum plaque for Epsten Group’s office building. Tell us about your space.
Our building, which we call “The Edge” for its Edgewood Ave. address, was a vacant industrial building from the 1940s. Its renovation for the 2011 LEED Platinum for New Construction certification included gutting it, adding significant insulation and an air barrier to all exterior walls and the roof, and installing a thin-film photovoltaic system on the roof. Then, in 2014, when we decided to go for LEED for Existing Buildings, we registered under the LEED v4 beta program and achieved our second LEED Platinum certification. Our real goal is to be LEED EB O+M recertified and to be a triple Platinum project—LEED NC and LEED EB O+M certified and recertified!
Atlanta is the epicenter for LEED buildings in Georgia, which made our Top 10 States for LEED list this year. We understand you’re on the Mayor’s radar now. Tell us why.
When we achieved LEED EB O+M v4 Platinum certification toward the end of 2014, I researched other buildings that had achieved this designation under LEED v4, and to the best of my knowledge, none had a prior LEED BD+C Platinum certification. So we are pretty sure that we were the first in the world to have Platinum certification under LEED BD+C and also under LEED v4 EB O+M. The City of Atlanta was elated to hear about it. Atlanta Mayor Kasim Reed is ambitious with his goals for sustainability, and we are in the Martin Luther King Jr. historic district, an up-and-coming area that is getting a lot of attention, particularly with the new streetcar that opened in December. You could say we’re a local business that has become the frontrunner for sustainability in Atlanta.
Your team took on a number of challenges with this project jumping from LEED for New Construction to LEED for Existing Buildings and from LEED 2009 to LEED v4. What were some of the biggest lessons learned?
Going into the LEED EB O+M certification, we knew that our prior LEED-NC v2009 certification was more about our building’s physical assets, and getting it set up for excellent performance. LEED EB O+M is about the performance of not just our building, but also of our entire business operations. Our 2011 LEED-NC v2009 achievement helped to set us up for success with subsequent LEED EB O+M certification and recertifications, however, LEED is constantly evolving, so if you go to the next LEED version, there are some gaps to be bridged. We participated in the LEED v4 EB O+M beta program, which offered an establishment review phase that we opted for and this helped with the transition from the 2009 rating system.
I think the biggest thing we learned was the value of clear communication and strong collaboration to achieve our energy and water saving goals. The materials credits also challenged us to do a fair amount of research into our supply chain and vendors to ensure that everything was happening according to our plans and policies. We learned to focus on products with multiple attributes, such as recycled content and local sourcing. This was especially important with expensive items, as they have a much greater effect on the percentage of compliance. In the end, this level of product scrutiny will most likely lead to more transparency in the marketplace.
If we had it to do over again, we might start LEED EB O+M within the first 12-18 months after the LEED NC certification, so our building knowledge and the LEED version of the prior LEED NC certification would be more current for the LEED EB O+M pursuit.
As a business owner and a CEO, how would you describe the benefits of achieving Platinum certification for LEED for Existing Buildings under v4 for your company?
We’ve seen important savings on our operational costs that will benefit our bottom line, but the best thing is that we have really transformed into a greener company inside and out.
One of our services is LEED consulting, and now our building is a teaching tool for our staff—everything from commissioning and energy tracking, to purchasing and operations. Now that we’ve completed the process, we can invite our clients to see a LEED double Platinum-certified building and say with confidence that we can competently perform similar services for our clients. Having this expertise is valuable to our company.
As the long term owner and occupant of The Edge, I was very glad to see that that all our initial energy and water efficiency measures that we implemented in our first LEED certification process and retested and verified with LEED EB have really paid off with superior energy and water savings. Our photovoltaic system has proven to contribute more to our energy needs than we first thought. We have also taken more advantage of renewable energy credits, and we‘ve committed to offset energy consumption through the purchase of additional RECs for a minimum of five years.
It was a great experience for staff too. We surveyed our staff about comfort and have fine-tuned the performance of the building through ongoing commissioning. Those involved with purchasing goods and services have worked closely with our vendors. It seems everyone is diligent in sorting solid waste, aided by good signage. We found that our alternative transportation commute benefit of $30 per month has resulted in significant adoption of alternative modes. We now are a very green company in all our operations and feel that we have great buy-in from our staff. We can really say that we walk the talk as a company.
As a LEED Fellow, I’m also proud that our group was a part of the LEED v4 beta program and completed the first establishment review in the world. We know that our experience will make the process better and easier for both GBCI reviewers and future project teams, and that overall we’ve contributed to the success of the LEED program.
So what’s next for Epsten Group and your building?
At Epsten Group, we enjoy being the frontrunner of sustainability and innovation. We are now eyeing the LEED Dynamic Plaque and the data tracking that goes into it, as well as subsequent LEED EB O+M recertifications.